Dimensions, design, geometric requirements and much more; in tube bending being able to achieve a minimum centerline radius can represent a considerable advantage. We are talking about extreme curvatures characterized by a ratio between centerline radius and diameter less than 1, which require significant technological know-how to be achieved.
In this article we will see:
- what are the technological parameters that make bending a tube difficult;
- what characteristics must a tube bender have to minimize the bending radius;
- how to calculate the difficulty ratio of a bend;
- a list of bent tubes with minimum centerline radius and their field of application
What are the technological parameters that make bending a tube difficult
There are multiple technological parameters that influence tube bending feasibility in steel, aluminum, copper or other metals.
First, it is good to consider the purely geometric aspects that characterize the curvature of the tube, its thickness and diameter, the centerline radius and the bending angle.
The extent of these factors defines a first-degree of difficulty ratio in creating the curve which we will talk about in the next paragraph.
The figure shows the main geometric parameters in tube bending: OD – Outside Diameter, WT – Wall Thickness, CLR –CenterLine Radius and BA – Bending Angle.
The feasibility of a bent tube obviously cannot stop at just calculating the difficulty ratio of the bend, but must consider many other aspects such as: bending angle, geometric complexity of the part, size of the tooling components and machine bending head, bending direction of the tube bender which can be right-hand or left-hand or right-hand and left-hand in the same cycle, any special tooling or particular machine cycles.
Moving beyond the purely geometric scope and especially when talking about tube bending with a high difficulty ratio, it is also necessary to consider the tube material, the type of lubrication, and the characteristics of the tube bender such as bending torque and thrust force.
What characteristics must a tube bender have to minimize the bending radius
Tube benders capable of obtaining greatly reduced centerline radii are machines capable of guaranteeing perfect control of the deformation of the tube material. This is only possible through constant control of the movement of the tube bending tools components and the forces it generates on the tube.
BLM GROUP's fully electric tube benders allow you to better control these parameters and in particular, in order to create a bend with a high difficulty ratio, they can manage the following during the bending cycle:
- mandrel position;
- pressure of the clamp die;
- thrust of the tube advancement;
- thrust and movement of the pressure die.
The skillful wizardry of these and other parameters allows you to manage extreme level bends even without any particular experience in tube bending.
Furthermore, in the event that wrinkles or imperfections occur on the bent tube, through VGPNext the operator can know which parameter to modify in order to resolve the defect that has arisen.
Find out more about VGPNext: the new generation software for programming tube bending machines.
How to calculate the difficulty ratio of a bend
Difficulty ratio in tube bending is the indicator that estimates in purely geometric terms the difficulty of creating a bend and is defined as the ratio between the diameter of the tube squared and the product between thickness and centerline radius.
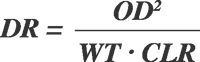
OD is the outside diameter
WT is the wall thickness
CLR is the centerline radius
In order to have a numerical reference value of the difficulty ratio of a bend, it is possible to state that a DR = 8 equates to a normally difficult bend which, to guarantee the absence of scratches, wrinkles or any small imperfection, requires the use of mandrel and wiper die.
Over the course of its over 60 years of experience in tube processing, BLM GROUP has developed the know-how necessary to create bends with minimum bending radii that are used in various industrial sectors.
In the next section some of the most interesting applications will be listed in detail with their relative difficulty ratio.
Do you have a part and want to know if it's feasible? Find out now!
List of bent tubes with minimum bending radius and their field of application
List of bent tubes with minimum bending radius and their field of application.
1. Component for car air conditioning system
Automotive sector
DR = 29
In the limited space available inside the engine compartment, the use of tubular components with minimum centerline radii allows compliance with space restrictions and precise adaptation to the layout prescribed by the engineer.
DR = 29 - tube with a diameter of 18 mm and a thickness of 1 mm, with a centerline radius of 11 mm.
2. Exhaust component
DR = 43
In order to maintain the aerodynamics of the vehicle, the exhaust components must be able to fit within the restricted spaces allowed by the chassis.
DR = 43 - tube with a diameter of 52 mm and a thickness of 1.5 mm, bent with a centerline radius of 42 mm.
3. Designer stool pedestal
Furniture sector
DR = 67
Extremely small centerline radius can define innovative shapes, with an attractive design and impeccable aesthetics as they have no welded joints.
DR = 67 - tube with a diameter of 110 mm and a thickness of 2 mm, curved with a centerline radius of 97 mm.