In questo articolo, è stato esaminato un caso pratico che illustra come l'adozione di impianti Lasertube, curvatubi e piegafilo, insieme ai relativi software di programmazione e integrazione, abbia permesso di risparmiare tempo e ridurre il consumo di materiali nella costruzione di una pensilina per biciclette.Il progetto dimostra come terzisti e carpenterie possano oggi beneficiare di questi moderni sistemi per la lavorazione di tubo e filo metallico per rendere più efficiente la realizzazione di strutture e telai tubolari.
-
- Descrizione del progetto e caratteristiche di progettazione della pensilina
- Semplificazione delle giunzioni attraverso l’uso di incastri e tagli piega
- Sostituzione di elementi complessi realizzati con lamiere tagliate, piegate e saldate assieme, con elementi tubolari più semplici
- Taglio laser e curvatura per ridurre il consumo di materiale
- Ottimizzazione del processo grazie al MES di gestione della produzione di BLM GROUP
1. Descrizione del progetto e caratteristiche di progettazione della pensilina
La pensilina in esame è una struttura per l’arredo urbano preposta al parcheggio di biciclette. Il telaio che la compone è costituito da tubi di diverso diametro, fili metallici e lamiere.
Modello 3D della pensilina prima della reingegnerizzazione.
In condizioni normali, il tempo di attraversamento previsto per questa struttura, ricorrendo a tecnologie produttive tradizionali, varia da 6 a 8 settimane, di cui 2 giorni sono necessari per l'assemblaggio dei componenti.
Questa prolungata fase di montaggio è principalmente attribuibile all'utilizzo di numerose maschere per la saldatura. I pezzi devono infatti essere preparati, accuratamente posizionati e infine saldati da personale esperto.
A prescindere dall’esperienza dell’operatore, a causa della complessità della struttura, il grado di precisione nell'assemblaggio finale rimane comunque limitato.
L’utilizzo delle tecnologie Lasertube, Curvatubi e Piegafilo di BLM GROUP ha permesso di semplificare tutto il processo produttivo attraverso la completa reingegnerizzazione del prodotto e la gestione ottimale di tutta la produzione.
Il risultato è una riduzione del 50% di mano d’opera, del 52% del tempo di produzione, del 26% dei costi di produzione e del 20% dei costi del materiale.
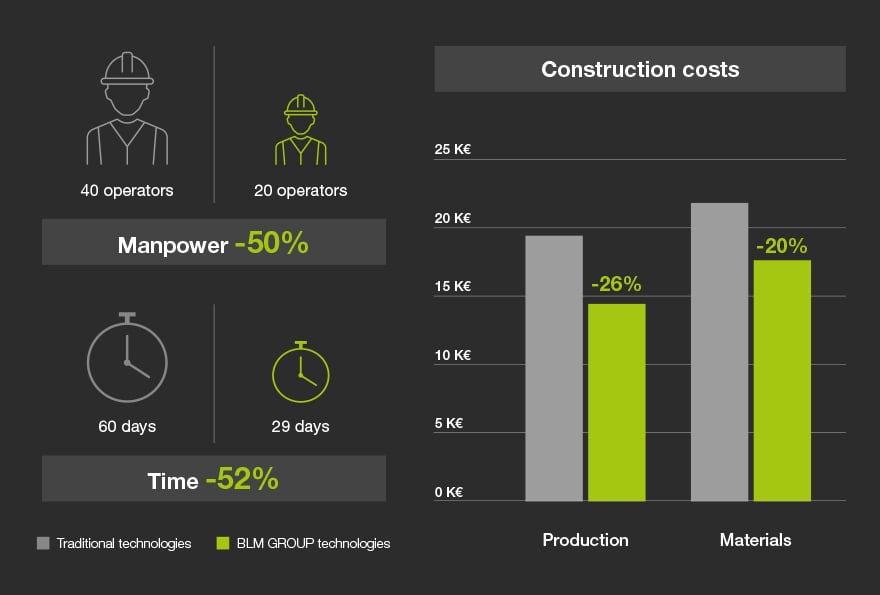
Quadro dettagliato del risparmio a seguito della reingegnerizzazione.
2. Semplificazione delle giunzioni attraverso l’uso di incastri e tagli piega.
L’utilizzo di incastri, fori passanti, uncini e tagli piega rappresenta un approccio efficace per semplificare la realizzazione del telaio.
Questo tipo di collegamenti garantisce un posizionamento preciso dei componenti facilitando così montaggio e saldatura e migliorando la precisione di tutta la struttura.
In questo progetto, il taglio laser del tubo ha permesso di creare incastri e giunzioni in modo estremamente preciso, semplice e pratico.
Un ruolo fondamentale in tal senso è stato offerto dal software di programmazione ArTube che offre un’ampia libreria di vincoli e incastri già pronti per essere applicati in modo parametrico nel modello CAD del pezzo da produrre.
Pensilina esposta durante la fiera Blechexpo presso lo stand di BLM GROUP.
3. Sostituzione di elementi complessi realizzati con lamiere tagliate, piegate e saldate assieme, con elementi tubolari più semplici
Nel progetto iniziale, gli elementi di supporto della rastrelliera erano composti da lamiere tagliate, piegate e saldate.
La loro realizzazione richiedeva l’utilizzo di tre macchine distinte: un impianto per il taglio della lamiera, laser o di altro tipo, una presso piegatrice e una saldatrice.
Grazie agli impianti Lasertube, questi elementi sono stati sostituiti da un unico componente ricavato da un tubo di sezione rettangolare tagliato al laser e piegato con la tecnologia di taglio piega.
Al posto delle tre macchine sopra menzionate è stato sufficiente utilizzare un solo impianto Lasertube.
Inoltre, l’introduzione di due semplici dentini ha consentito il posizionamento preciso durante l’assemblaggio, semplificando la successiva saldatura del pezzo al pilone di supporto del tetto.
Elemento di sostegno della rastrelliera prima e dopo l’introduzione della tecnologia Lasertube.
4. Taglio laser e curvatura per ridurre il consumo di materiale
Cave e dentini hanno rivestito un ruolo cruciale anche nella realizzazione della rastrelliera.
Il tubo di supporto trasversale è stato infatti provvisto dei fori e delle aperture necessarie ad ospitare i tubi e i tondini curvati che avranno lo scopo di sostenere le biciclette.
Questa soluzione ha non solo semplificato il montaggio e la saldatura dei componenti, ma ha anche permesso di risparmiare materiale riducendo la lunghezza dei tondini.
Tuttavia, la riduzione del consumo di materiale non solo è il risultato di un generale alleggerimento della struttura, conseguente alla sua reingegnerizzazione, ma anche all'impiego della tecnologia All-In-One, che adatta la posizione delle geometrie di taglio per compensare gli effetti deformativi della curvatura. Grazie alla tecnologia All-In-One è stato possibile eliminare gli sprechi e ottenere tubi tagliati al laser e curvati giusti fin da subito.
Scopri di più sulla tecnologia All-In-One.
5. Un processo ottimizzato grazie al MES di gestione della produzione di BLM GROUP
I software di progettazione CAD/CAM (ArTube per le macchine Lasertube e VGPNext per le curvatubi e le piegafilo) hanno svolto un ruolo essenziale nella reingegnerizzazione del prodotto, dall’importazione dei modelli 3D, all’ottimizzazione dei componenti fino alla creazione dei programmi pezzo per gli impianti di taglio laser e curvatura.
Attraverso il Manufacturing Execution System (MES) di BLM GROUP, l’intero ciclo produttivo è stato gestito in modo integrato e flessibile, trasferendo le commesse di produzione agli impianti coinvolti, pianificando le attività con evidenza dei tempi precisi di lavorazione, assegnando le priorità di esecuzione e specificando i materiali da usare.
L’esposizione chiara ed intuitiva dei dati ha permesso di migliorare tutto il processo produttivo, ha ridotto i tempi di progettazione, azzerato gli sprechi di materiale e minimizzato le inefficienze.
Una rigorosa schedulazione delle commesse e l’esatta stima dei tempi di produzione hanno consentito di offrire rapidamente un preventivo preciso dell’intero progetto a partire dall’assieme 3D del prodotto, mentre il controllo in tempo reale degli impianti ha permesso di mantenere alte le performance di produzione e di intervenire prontamente in caso di fermi.
Scopri il MES di produzione di BLM GROUP.