Dieser Artikel zeigt anhand des Beispiels eines Fahrradunterstandes auf, wie sich in der Produktion mit Rohrlasern der Lasertube-Familie, Rohrbiegemaschinen und Drahtbiegemaschinen in Kombination mit der zugehörigen Programmier- und Integrations-Software Zeit sparen und der Materialverbrauch reduzieren lassen.
Das Projekt macht deutlich, wie Zulieferer und Architekten mit Hilfe innovativer Maschinen für die Verarbeitung von Rohren und Draht die Effizienz in der Herstellung von Stahlkonstruktionen und Rahmen aus Rohren erhöhen können.
-
- Projektbeschreibung und konstruktive Merkmale des Fahrradunterstandes
- Vereinfachte Verbindungen unter anderem mit Hilfe von Trenn-Biegeschnitten
- Austausch komplexer Komponenten aus geschnittenem, gebogenem und zusammengeschweißtem Blech gegen einfache Rohrelemente
- Rohrlaserschneiden und -biegen, um den Materialverbrauch zu verringern
- Optimierter Prozess dank des Produktions-Managements mit dem MES der BLM GROUP
1. Projektbeschreibung und konstruktive Merkmale des Fahrradunterstandes
Bei diesem Unterstand handelt es sich um eine öffentliche Außenanlage für das Unterstellen von Fahrrädern. Der Rahmen besteht aus Rohren verschiedener Durchmesser, Metalldraht und Blech.
3D-Modell des Fahrradunterstandes vor der Neugestaltung.
Wird eine solche Konstruktion mit konventioneller Technik produziert, beträgt die zu erwartende Vorlaufzeit im Normalfall sechs bis acht Wochen. Zwei Tage werden für die Montage der Komponenten benötigt.
Diese lange Montagezeit ist in erster Linie auf die vielen Schweißverbindungen zurückzuführen. Die Teile müssen sorgfältig vorbereitet, positioniert und anschließend von fachkundigem Personal geschweißt werden.
Auch wenn die Maschinenbediener über viel Erfahrung verfügen, ist es angesichts der Komplexität der Konstruktion eine Herausforderung, in der Endmontage Genauigkeit zu erreichen.
Dank des Einsatzes eines Rohrlasers sowie von Rohrbiege- und Drahtbiegemaschinen der BLM GROUP konnte der gesamte Produktionsprozess des komplett neu gestalteten Unterstandes signifikant vereinfacht werden.
Der Arbeitsaufwand wurde halbiert und die Produktionszeit um 52 %, die Produktionskosten um 26 % und die Materialkosten um 20 % reduziert.
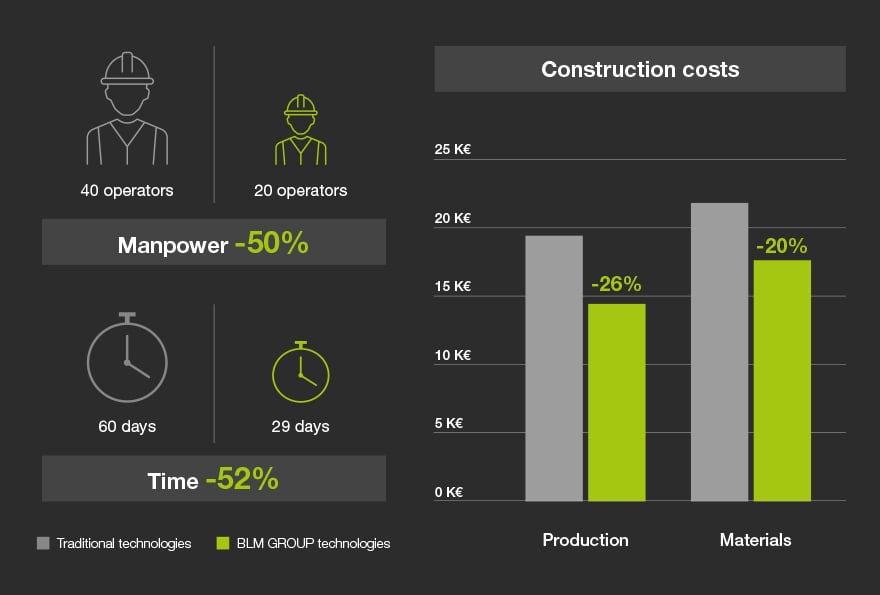
Das Schaubild zeigt detailliert die Einsparungen, die dank der Neugestaltung des Fahrradunterstandes erzielt werden konnten.
2. Vereinfachte Verbindungen unter anderem mit Hilfe von Trenn-Biegeschnitten.
Die Konstruktion des Rahmens wurde mit innovativen (Steck-)Verbindungen, Verzahnungen und Trenn-Biegeschnitten deutlich vereinfacht.
Verbindungen dieser Art ermöglichen das genaue Zusammenfügen der Komponenten, was wiederum die Montage erleichtert, den Schweißaufwand verringert und die Genauigkeit der gesamten Konstruktion verbessert.
Bei diesem Projekt ermöglichte das Rohrlaserschneiden auf einfache Weise die Realisierung äußerst genauer Verbindungen.
Die ArTube-Programmier-Software der Rohrlaser der Lasertube-Familie der BLM GROUP spielte dabei eine entscheidende Rolle. Sie wartet mit einer umfassenden Bibliothek mit Verbindungen auf, die parametrisch in CAD-Modelle herzustellender Teile übernommen werden können.
Fahrradunterstand auf dem Blechexpo-Messestand der BLM GROUP.
3. Austausch komplexer Komponenten aus geschnittenem, gebogenem und zusammengeschweißtem Blech gegen einfache Rohrelemente.
In der ursprünglichen Konstruktion wurden die tragenden Elemente des Gestells aus geschnittenem, gebogenem und geschweißtem Blech zusammengesetzt.
Ihre Herstellung erforderte den Einsatz von drei verschiedenen Maschinen: einer Blechschneidemaschine (Laser oder eine andere Technik), einer Abkantpresse und einer Schweißmaschine.
Dank der Rohrlaser der Lasertube-Familie konnten diese Elemente gegen ein einziges Bauteil ersetzt werden. Dieses wurde aus einem Rechteckrohr mit Trenn-Biegeschnitten hergestellt.
Statt der drei oben genannten Maschinen genügte der Rohrlaser.
Darüber hinaus ermöglichten zwei einfache Zähne das genaue Positionieren in der Montage, was das anschließende Schweißen des Werkstücks an den Dachpylon vereinfachte.
Gestell-Trägerelement vor und nach dem Umstieg auf die Technik des Rohrlaserschneidens.
4. Rohrlaserschneiden und -biegen, um den Materialverbrauch zu verringern.
Auch Schlitze und Zähne spielten bei der Konstruktion des Gestells eine entscheidende Rolle.
Das querverlaufende Stützrohr weist Bohrungen und Schlitze auf. Diese nehmen die gebogenen Rohre und Stangen auf, mit denen die Fahrräder gestützt werden.
Diese Lösung hat nicht nur die Montage und das Schweißen der Bauteile vereinfacht. Vielmehr wird auch Material eingespart, da die Längen der Stangen verringert werden konnten.
Der geringere Materialverbrauch resultiert jedoch nicht nur aus der neu gestalteten, schlankeren Konstruktion. Er ist auch auf die All-In-One-Technik zurückzuführen. Diese passt die Geometrien im Rohrlaserschneiden so an, dass die im Biegeprozess auftretenden Verformungen kompensiert werden. Das heißt, es können auf Anhieb einwandfrei lasergeschnittene und gebogene Rohre produziert werden. Damit fällt auch der Abfall weg, der bei den ansonsten erforderlichen Testbiegungen entsteht.
Erfahren Sie mehr über die All-in-One-Technik.
5. Optimierter Prozess dank des Produktions-Managements mit dem MES der BLM GROUP
CAD/CAM-Programmier-Software (ArTube für die Rohrlaser und VGPNext für die Rohrbiege- und Drahtbiegemaschinen der BLM GROUP) spielte bei der Neugestaltung des Unterstandes eine wesentliche Rolle – angefangen beim Import der 3D-Modelle über die Optimierung der Komponenten bis hin zur Erstellung der Teileprogramme für das Laserschneiden und das Biegen.
Mit dem Manufacturing Execution System (MES) der BLM GROUP wurde der gesamte Produktionsprozess ganzheitlich und flexibel gesteuert: Übermittlung der Arbeitsaufträge an die beteiligten Maschinen, Planung der Arbeitsschritte mit Nachweis der exakten Durchlaufzeiten, Zuweisung der Prioritäten in der Verarbeitung und Bestimmung der eingesetzten Materialien.
Die übersichtliche und intuitive Darstellung der Daten verschlankt die Produktionsprozesse, indem sie die Konstruktionszeiten verkürzt, die Vergeudung von Material ausschließt und Effizienzverluste minimiert.
Sorgfältige Auftragsplanung und genaue Vorabberechnung der Produktionszeiten ermöglichten eine schnelle Kalkulation des gesamten Projekts – angefangen bei der 3D-Montage des Produkts. Gleichzeitig ermöglichte die Steuerung der Maschinen in Echtzeit eine gleichbleibend hohe Produktionsleistung und ein schnelles Eingreifen bei Maschinenstillständen.
Weitere Informationen zum MES der BLM GROUP.